
To get the default value for posting change like warehouse process type 4020, BC set activation is performed for /SCWM/INTERNAL_WH_PROCESS.ģ. To get scrapping warehouse process type 4020, BC set activation is performed for /SCWM/WT_PROCESS_TYPE.Ģ. I have mentioned some of the key BC sets as below:ġ. Note that if our pre-installed EWM warehouse 0001 doesn’t provide the scrapping process related key set-ups, then BC set activation is required to get basic warehouse process type for scrapping and the related default values for posting change including scrapping storage type.
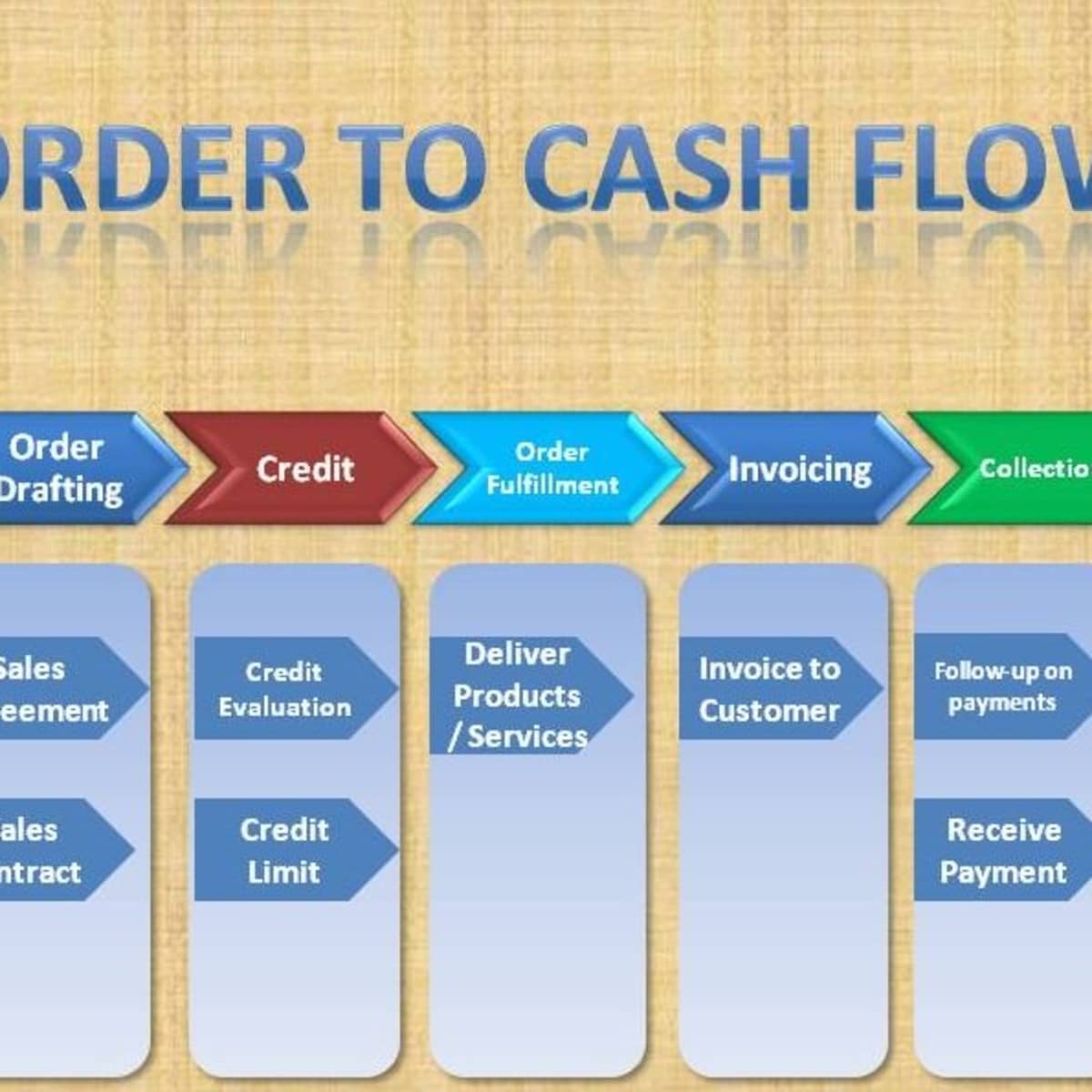
Variant 2: Scrapping the product due to damaged stock using RFUI Variant 1: Scrapping the product due to expired shelf life of the batch In the blog, I will explain how EWM can help to execute the scrapping and write-off process in both these process variants, I have taken total batch quantity scrapping as an example in order to run system steps for both the variants: If the product is found damaged and it carries no resale value, it is also usually written-off from the Inventory books by posting it’s value against cost center. If the batch is expired, typically in Food, Pharmaceutical & Health industry, the product is neither good for the production usage nor suitable for the human consumption and hence one can not sell such expired products to earn the salvage money out of the scrapped material thus it is typically written-off from the Inventory books by posting it’s value against cost center. Due to expiration of the product/batch itself 2. Scrapping could be typically required due to two main reasons: 1.
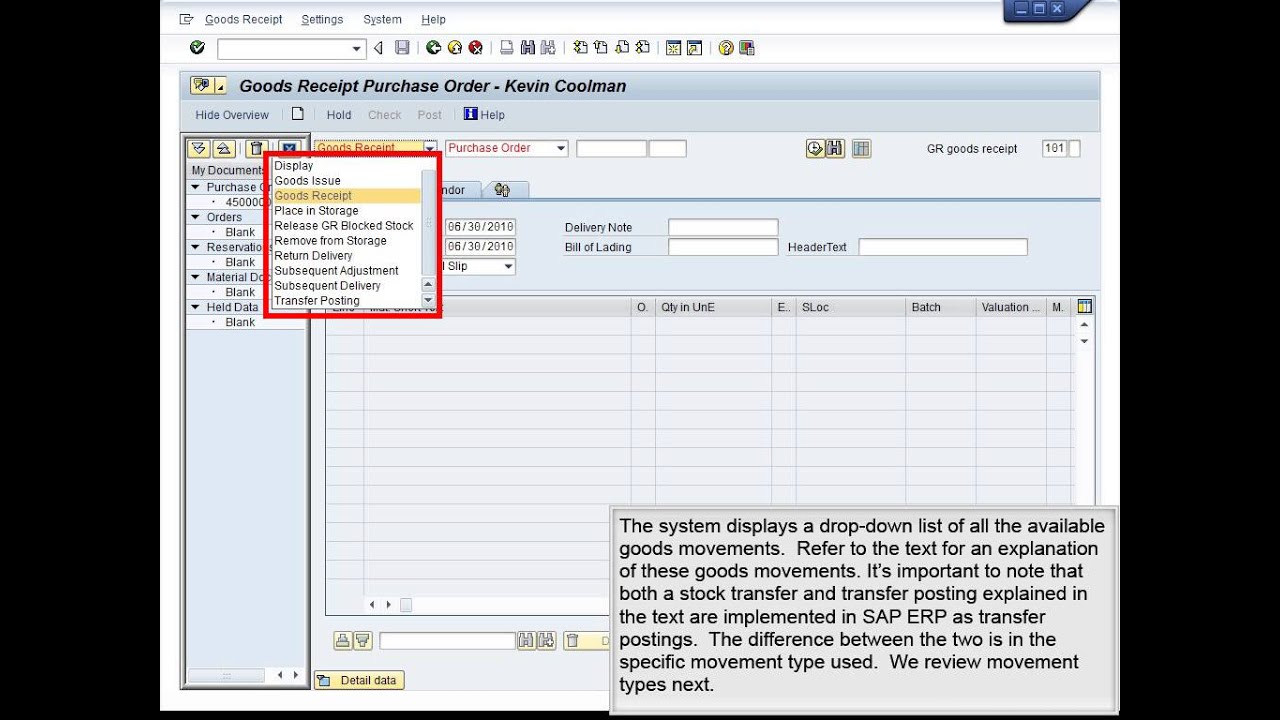
Executing the Goods Issue to Scrapping cost center. Moving the stock from storage bins to the scrapping zone or quarantine area 2.

Scrapping process inherently will consist of two parts: 1. This will have financial implications as the stock which is written-off has dollar value. Scrapping process is an Internal warehouse process in which stock of the material is written-off from Inventory books (if not sold). If you want to involve MRP, you have to go via stock: Create a reservation for a goods issue to a cost center (movement type 201), let MRP generate a purchase requisition (without account assignment), and, after receipt of the material, post a goods issue to the cost center (with reference to the reservation).In this blog, I will share with you my experience of executing different scrapping process variants in Decentral-EWM system on S/4 HANA 1909. Purchase requisitions for cost centers should be created manually (or via an interface e. But if you change the account assignment category to something like K, the purchase requisition will not affect the stock/requirements situation anymore, so a new purchase requisition will be proposed during the next MRP run.

Once a purchase requisition proposed by MRP has been saved, it can be changed, using any account assignment category. When you try to change a purchase requisition proposal during the MRP run, you can only enter an account assignment category that has special stock indicator E (sales order stock) or Q (project stock). Purchase requisitions with account assignment category K are used for purchasing material for a cost center, without ever hitting stock.Īccordingly, MRP only creates purchase requisitions for normal stock, for sales order stock or for project stock. MRP is about planning stock: normal stock, sales order stock or project stock.
